Our capstone team at Brigham Young University designed and built a Mars rover capable of performing a myriad of tasks in preparation for the University Rover Challenge (URC).
The Challenge
The URC challenge, held at the Mars Desert Research Station in southern Utah, consists of four critical missions:
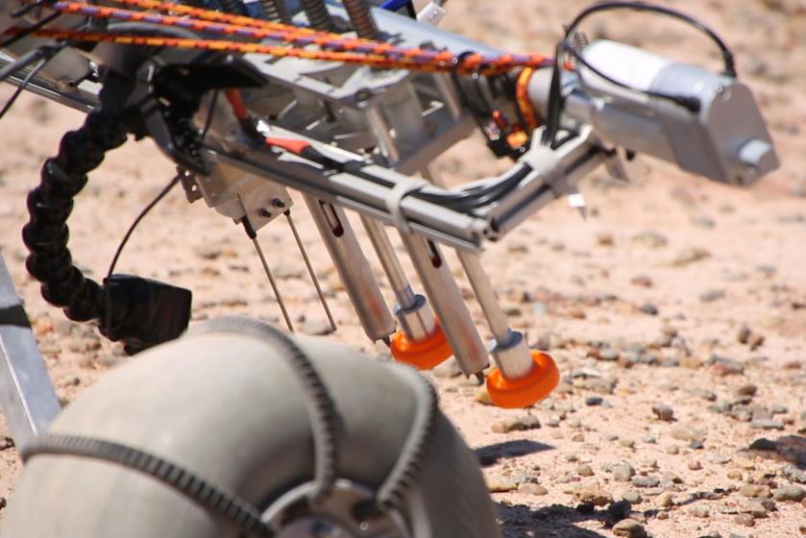
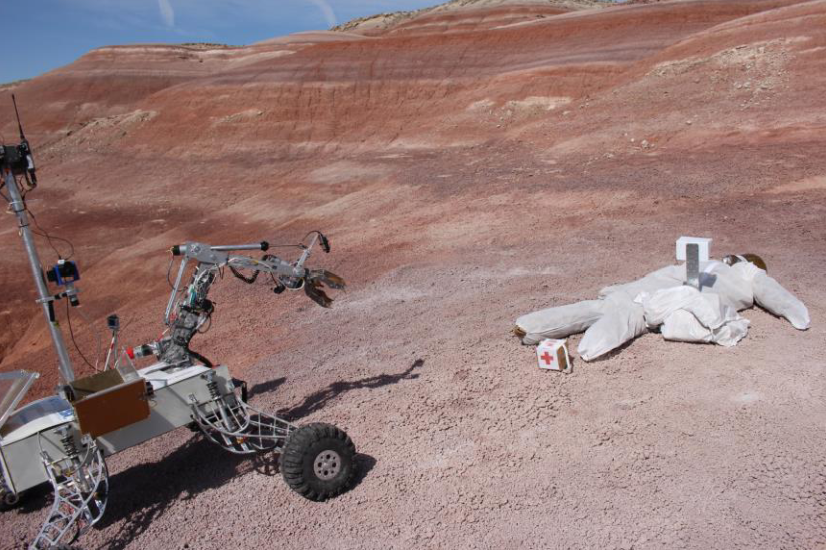
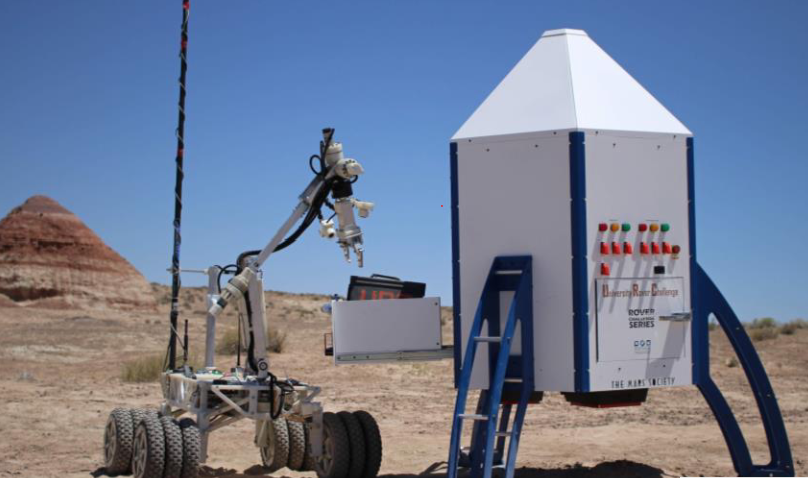
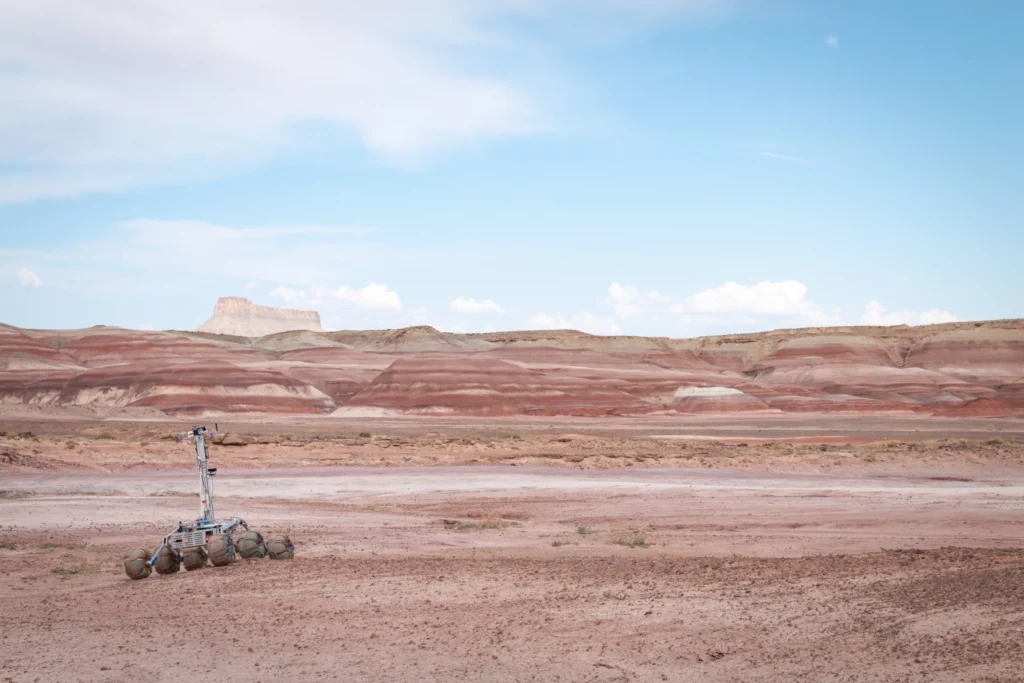
Space Configuration Challenges
Among the many challenges we (the mechanical team) solved while improving the rover’s subsystems (manipulation, mobility, and modularity), one was particularly critical: new URC regulations required all rovers to fit within a compact 1.2-meter cube during weigh-in, simulating storage conditions aboard a Mars-bound rocket. Our existing rover exceeded these dimensions in both height and length, presenting us with a critical decision. Rather than starting from scratch, we embraced the challenge of modifying our current design to meet these new constraints while preserving its core functionality.
(2.a.ii) “Rovers shall be weighed by the judges during the set-up time of each mission. For weighing the rover must fit completely within a 1.2m x 1.2m x 1.2m box. Rovers may be placed in any orientation, and articulate/fold/bend to fit within the transport crate, but may not be disassembled to do so. This includes wheels, antenna, and any other system protruding from the rover. Failure to fit within the specified dimensions at weigh-in will result in a 40% penalty. After weighing, rovers may unfold/expand to any size.”
Folding Wheel Assembly
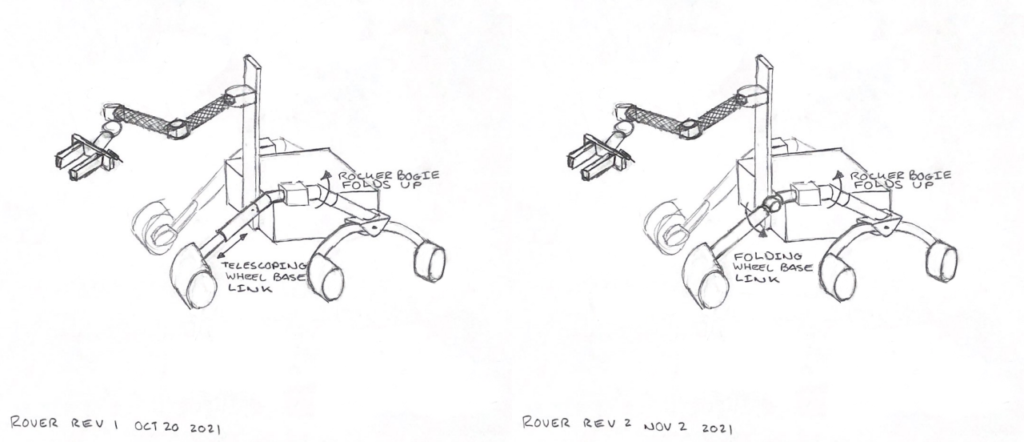
The key challenge lay in our rocker-bogie suspension system, which was essential for the rover’s stability. This wheeled structure, while providing crucial balance across rough terrain, was the main reason our rover exceeded the size limits. We needed a solution that would preserve the wide wheel base during operation but still meet the new size requirements.
Our breakthrough came in the form of a folding mechanism. We designed the wheel assemblies to fold inward during transport, wrapping around the central electrical housing when stowed. This origami-like transformation allowed us to maintain the rover’s wide, stable stance during operation while achieving a compact form for weigh-in, with the electrical box resting on the ground and the wheels tucked efficiently around it.
Folding Mechanism Clamp Design
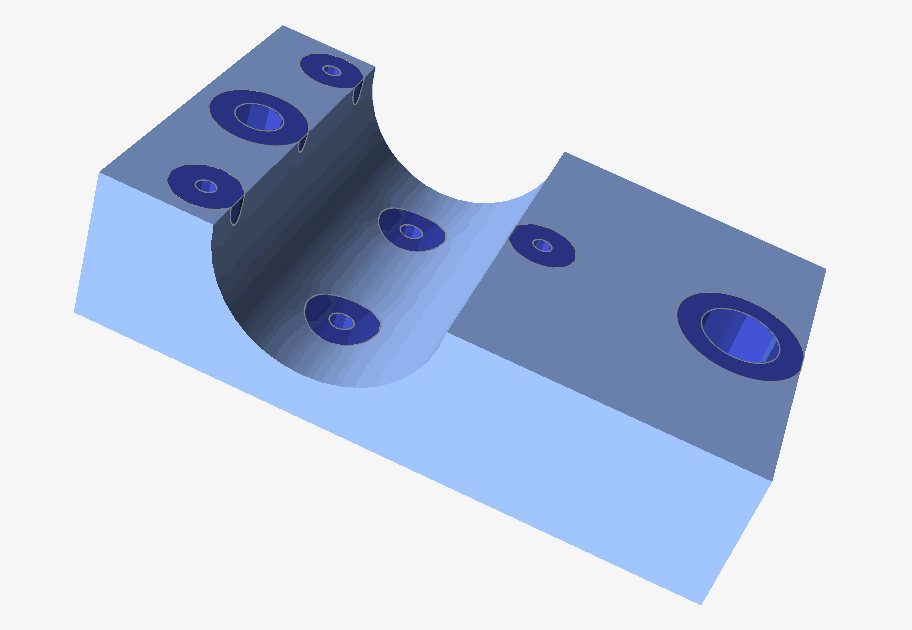
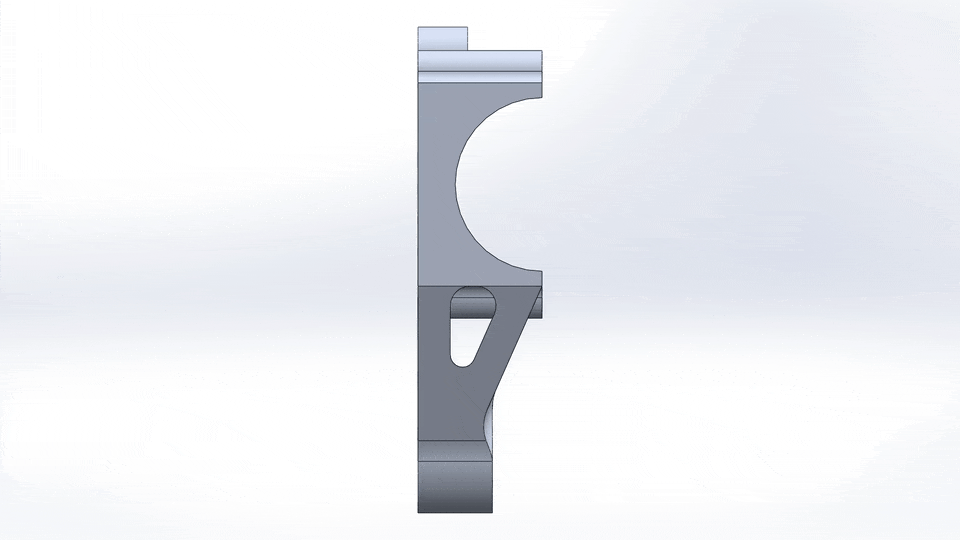
Folded Configurations
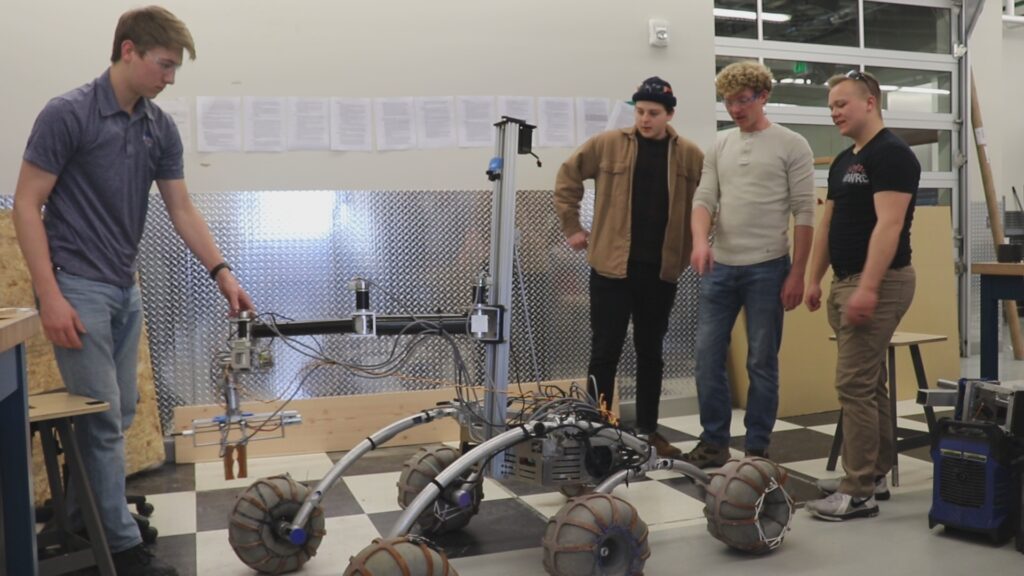
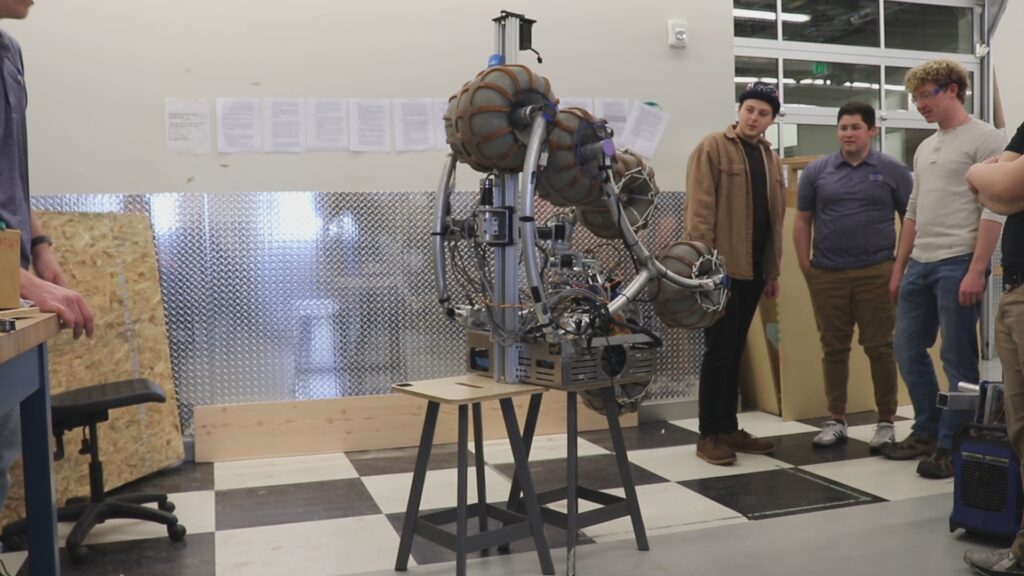
Elevator Redesign
With the footprint issue solved, we turned our attention to the rover’s height problem. The main culprit was our linear elevator system, which worked in tandem with our SCARA-configuration robotic arm. We had chosen the SCARA design for its excellent maneuverability, but it came with a trade-off: the arm could only move horizontally, relying entirely on the elevator mechanism for any vertical movement. This meant the elevator needed significant height to ensure the arm could reach tasks at various elevations. Finding a way to reduce the elevator’s height while maintaining its functional range became our next critical challenge.
Our solution involved a complete redesign of the elevator system to maximize its effective range within the new 1.2m height constraint. We replaced the traditional direct-drive motor setup with an innovative belt and pulley system mounted at 180 degrees, which reduced the space needed for the drive mechanism from 156mm to just 28.35mm. The team sourced components, including a C-Beam linear rail cut to exactly 1.15m and compatible mounting plates, to eliminate the binding issues that had plagued the previous design. This optimization allowed us to achieve a maximum gripper height of 1.531m when deployed while maintaining the rover’s collapsed height under 1.2m during weigh-in. To ensure smooth operation, we added proper bearings and precision-aligned components throughout the system, resolving the mechanical binding issues that had affected the previous design.
Motor Mounting Setup
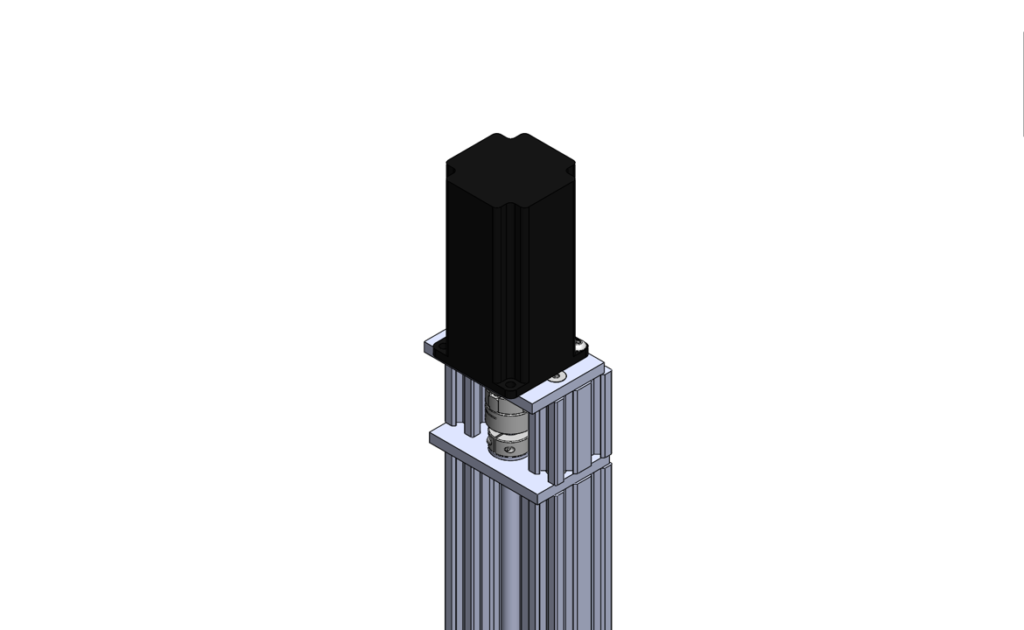
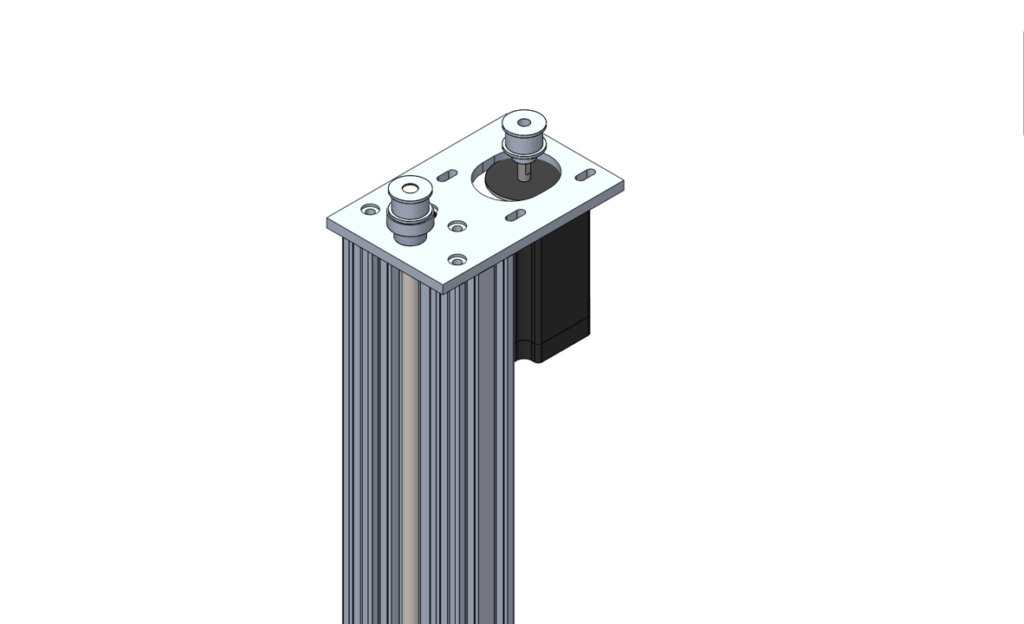
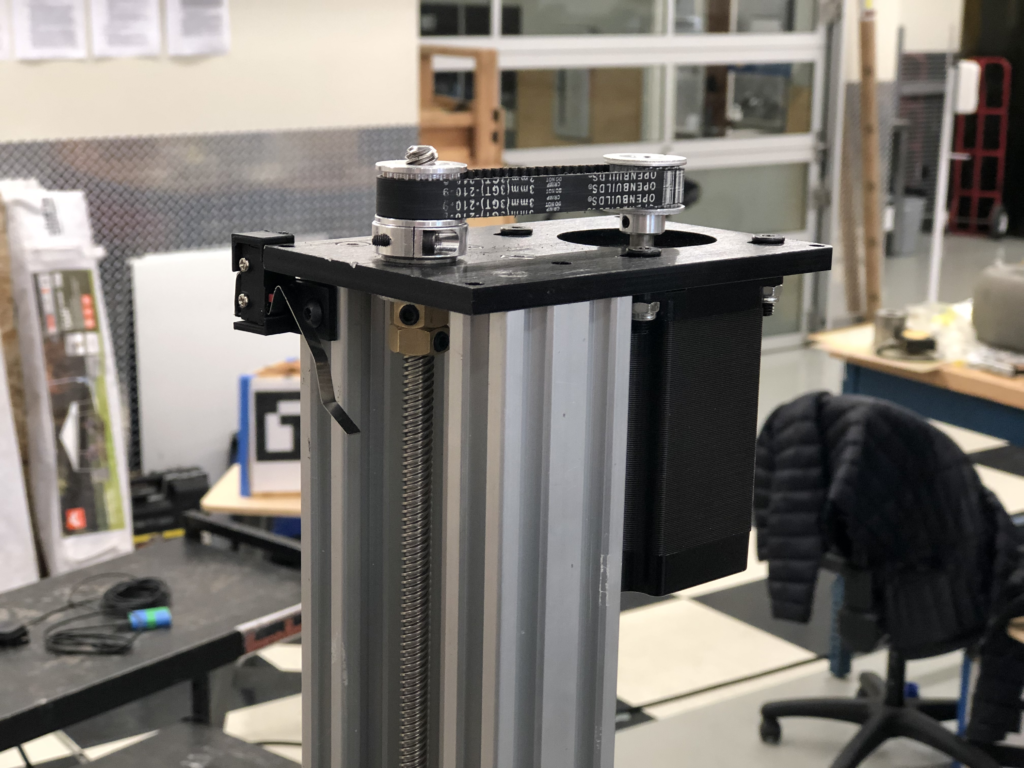
Result
The redesign of the elevator and the folding wheel assembly proved to be highly successful, meeting both functional and design objectives. These improvements enhanced the overall performance, reliability, and ease of transport for the system. The official weigh-in results, which validated the effectiveness of the redesign, can be viewed in the accompanying video.