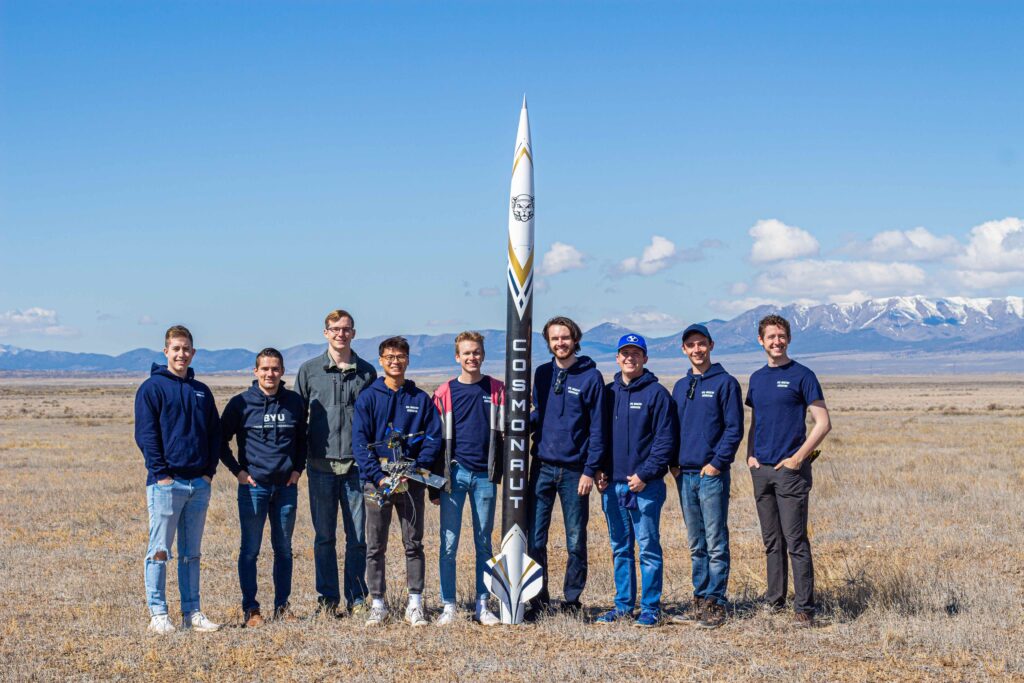
As team lead for BYU Rocketry‘s Experimental High-Power Team, I directed a multi-disciplinary project that challenged both my technical and leadership abilities across two semesters. Leading a nine-person team split across three specialized sub-teams (Payload, Guidance Navigation & Control, and Structures), I managed the development of a Level 3 high-power rocket designed to precise competition standards. Our technical objective – delivering an 8-pound payload to exactly 10,000 feet – required careful coordination between drone payload systems, air brake development, and structural engineering.
Project Management
As team lead, I worked to hold each sub-team accountable for their work by establishing weekly meetings with time devoted for progress report, work projection, and deliberation. I worked jointly with my team and the BYU Rocketry Association presidency to establish challenging yet feasible project deadlines that would keep team members working hard, but also ensuring that all necessary work would be done with a significant buffer for unexpected delays. Throughout the project, I maintained professional documentation through preliminary and critical design reviews, which included analysis of budget allocations, bills of materials, failure mode analysis, and simulation data. This documentation not only kept stakeholders informed but also helped our team maintain a clear vision of our technical objectives and project status.
Subsystem Engineering
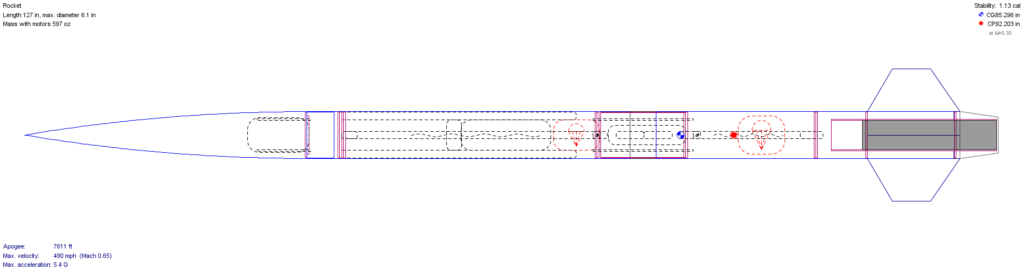
Structures
The structures subsystem required precision manufacturing and innovative solutions to meet our design requirements. Carbon fiber body tube fabrication proved particularly challenging – our initial attempt resulted in significant warping, but refined processes led to two successfully manufactured tubes. To ensure precise fin alignment, we developed a specialized router jig system that dramatically improved upon traditional handheld cutting methods. This allowed us to create perfectly straight, parallel fin slots along the body tube’s length. The final assembly integrated through-wall fins secured with epoxy, using laser-cut jigs to maintain exact 90-degree alignment during curing. Additional structural elements included precisely machined brass rail buttons and carefully sized air brake slots, all critical to the rocket’s flight performance and stability.
Guidance, Navigation, and Control
The Guidance, Navigation, and Control team tackled the critical challenge of ensuring our rocket would hit its exact 10,000-foot target apogee while maintaining stable flight and safe recovery. At the core of this system was an active air brake mechanism designed to provide real-time flight path adjustments. The avionics bay housed dual flight computers for redundancy, along with the air brake control system. Recovery system development involved extensive testing to determine optimal ejection charge quantities and parachute deployment sequences. Through multiple ground tests, we fine-tuned the black powder charges and shear pin configurations to achieve reliable separation between stages. The team also integrated GPS tracking capabilities into the nose cone, enabling accurate location and recovery of the rocket after flight.
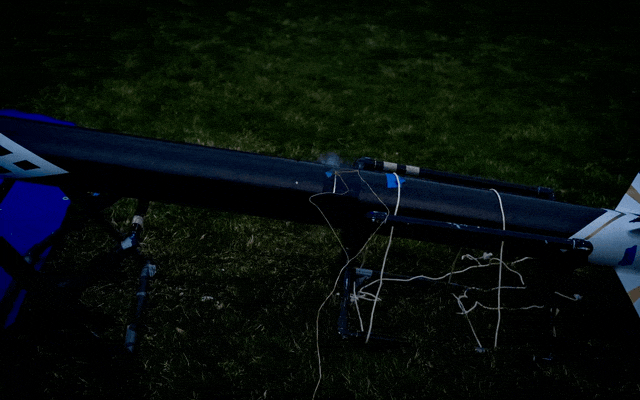
Payload
The payload team developed an innovative deployable drone system designed to be ejected from the rocket at apogee. This complex subsystem integrated both the drone itself and a deployable ground station, requiring careful consideration of space constraints and deployment mechanics. The team’s scope included not only the mechanical design and fabrication of both components but also the development of custom software for drone operations and ground control systems. A critical challenge was ensuring reliable deployment and establishing robust communication between the drone and ground station post-ejection. The system required precise integration with the rocket’s main deployment charges and careful placement within the upper body tube to guarantee successful ejection during flight.
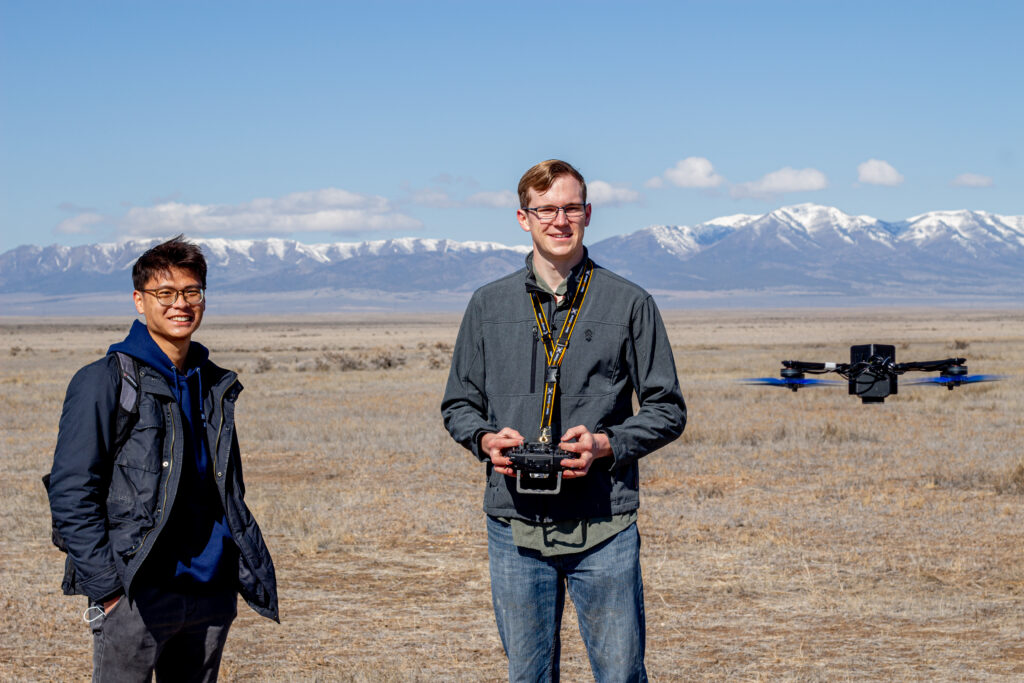